23 Feb 2023
FULGAR & POMPEA A VIRTUOUS HISTORY FOR A SUSTAINABLE TEXTILE SUPPLY CHAIN
Sustainability and innovation are the keywords of the corporate path of Made in Italy excellence in the world of underwear and hosiery.
An almost unique case history where a young second-generation entrepreneur, sensitive to issues such as sustainability and the circular economy, skilfully combines the excellence of Italian manufacturing with technological development and research. A path that revolutionizes both the production of yarns and the product for the final consumer. It is the story of Alan Garosi - Co-owner and Head of Marketing of the Fulgar group and Pompea‘s since 2019.
A story that demonstrates that starting from the choice of innovative materials and production processes, an entire supply chain can be born oriented towards sustainability and an offer of products that meet the new demands of consumers.
During the opening ceremony of Filo - the international exhibition of yarns and textile fibers that opened yesterday at the MiCo in Milan - with the theme "Sustainability, traceability and supply chain - The right connection between the raw material and the finished product of the Exhibition", Alan Garosi recounted the evolution of the processes and strategies of his companies, Fulgar and Pompea: “It all started with Fulgar where sustainability has been one of the company's key assets for over a decade with constant investments that have led to the efficiency of production processes and partnerships with the world of technological innovation that have made possible the creation of an entire green portfolio. The Q-CYCLE® yarn, obtained through a process that transforms post-consumer plastic waste into pyrolysis oil, derives from the recycling of end-of-life tires and represents its latest novelty.”. Garosi goes on saying: “A unique expertise gained in Fulgar which also guided me in the development strategy of Pompea, the group brand which is also a protagonist in sustainability and re-cycling. Every material used in the production, in fact, is processed so that it can have a second life. The company thus recycles over 80% of what enters the production process.”.
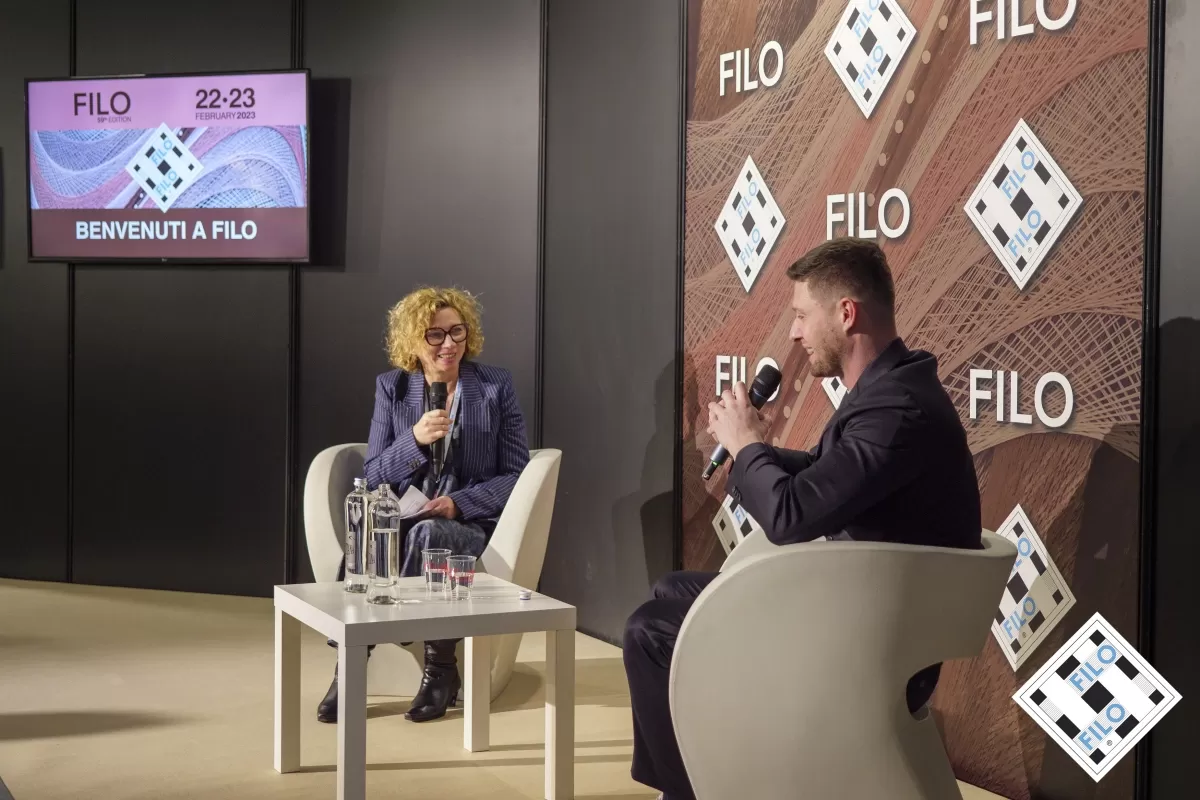